What are anodes and how do they work?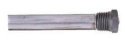
An anode is made from a less noble metal than any other metal in the system. This is usually called a Sacrificial Anode so this corrodes instead of valuable equipment. Magnesium and aluminium are less noble than steel, which is why they are used for anode rods.
Sacrificial anodes have been in common usage in a multitude of applications for many years. They protect all ships at sea and above ground pipelines, boilers, hot water heaters and generally steel structures immersed in water or damp soil conditions where corrosion could be a problem.
The corrosion (rust) is the result of electrolytic action travelling through moisture or fluid to home in on the metal surface at risk. Depending upon the existing conditions such as amount and quality of the fluid and the effective presence of any other protective coating on the metal surface, the rate of anode corrosion can vary substantially.
For fresh and groundwater applications our anodes are of a particular grade of magnesium which is “electro-negative relative to steel” which means that they will attract the destructive electrolytic action on to themselves. This type of galvanic protection is called sacrificial and the principle of electrolytic corrosion control is called cathodic protection. Because cathodic surfaces cannot rust, the steel surface is protected.
Riddlesdown Anode Manufacturing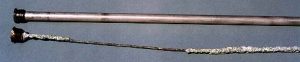
Riddlesdown Manufacturing specialises in making superior special application anodes: the 1-off or the no-one-else-wants-to-do anodes – all completed quickly and efficiently. We also make anodes specific to your drawings and specifications. Be it for water chillers, heat exchangers, boats, bores, pumps, casings, tanks, steel vessels, sheds, or anything metal needing anodes, call Riddlesdown Manufacturing for help.
Anodes manufactured by Riddlesdown Manufacturing are made from magnesium alloy with a mild steel threaded plug and are welded on the joint where the steel core passed through the plug. When all of the magnesium has been used up and the anodes useful life is over, the steel wire core is left attached to the steel plug and is removed when the anodes are changed.
Anodes made by some other manufacturers have the magnesium rod simply pressed into a brass plug, and as soon as these anodes are put into service the magnesium starts to corrode where it comes into contact with the superior material of the brass hollow plug. In a very short time the anode becomes loose and falls out of the plug. This results in either rattling around in the turbulent water, chipping and damaging the coating on the condenser ends, or they can be drawn into the circulating pumps where it will cause varying degrees of damage to the pump impellers as it is chopped up. These bits can travel around the system until they find valves and control units, causing them to fail.
The longer series anodes produced by Riddlesdown Manufacturing have an additional thread cut into the inside of the plug to prevent the steel cored magnesium component coming adrift. Magnesium is the most-used metal for the manufacture of sacrificial anodes. It can be used in many applications: fresh water, chemically treated water and direct earth burial to name a few.
The magnesium pencil anodes made by Riddlesdown Manufacturing specifically for condenser ends and heat exchangers are available in a variety of sizes and lengths. The most popular anodes have one end plain and one end threaded and fitted to a hex head: 1/4″, 3/8″, 1/2″, 3/4″ or 1.00″ B.S.P. anode plug (sometimes called a spud). All anodes can be made and supplied to any length required. These are all available for same-day delivery.
Block and disc anodes are available in various sizes. These can be machined overnight to fit any size required for delivery the next day.
Gaskets are also supplied in Nebar, rubber and cork – custom cut to fit individual machines. These are cut overnight where possible and delivered the next day. If urgent, same-day cut and delivery is available.
We also refurbish chiller ends, water box’s, condenser ends, repair and rebuild divider plates, fit new bushes – replacing corroded anode socket threads, grit blast ends and recoat – returning with gaskets if needed, anodes fitted, ready to bolt back onto the machine, all within approximately 7 days or less.